Case
Study by DaimlerChrysler
Internal
Flow through a Water Pump
The purpose of a recent study performed by DaimlerChrysler
was to compare the performance of Harpoon-based CFD against previous solutions
using tetrahedral meshes.
The effect of mesh skew on accuracy and convergence
was observed. 14 operating cases were simulated: 1000-7500rpm at
500rpm increments. Inlet velocities were derived based on the test mass flow
measurements. Pressure rise & flow split between volutes were solved. Excellent
agreement was obtained using a Harpoon mesh, containing approximately 3M cells,
at a fraction of the simulation effort required for a full tet mesh. The
following was concluded from this effort:
- The
hexa-dominant mesh improves the convergence quality & rate of the model,
even with reduced mesh resolution
- Mass
conservation residuals dropped by up 90%
- Kinetic
Energy residuals dropped by up to 20%
- Convergence
time was reduced by more than 30% for the initial condition case, up to 80% for
the consecutive cases
Details of the model are shown in figure 1. A close-up of
mesh details is shown in figure 2. Figures 3 and 4 compare results for
Harpoon meshes (blue) against tet mesh results (magenta). (all data courtesy
DaimlerChrysler)
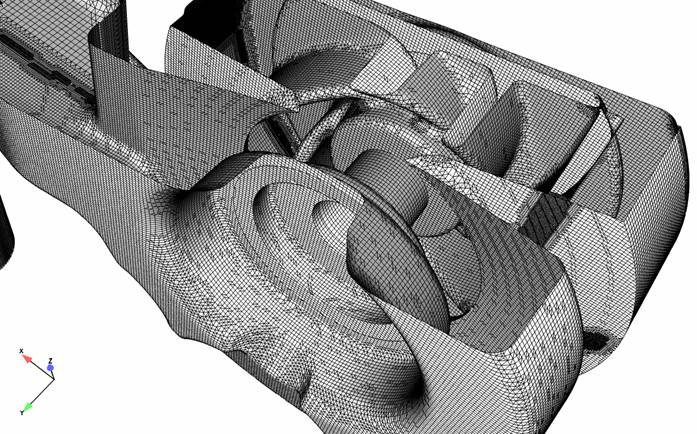

|